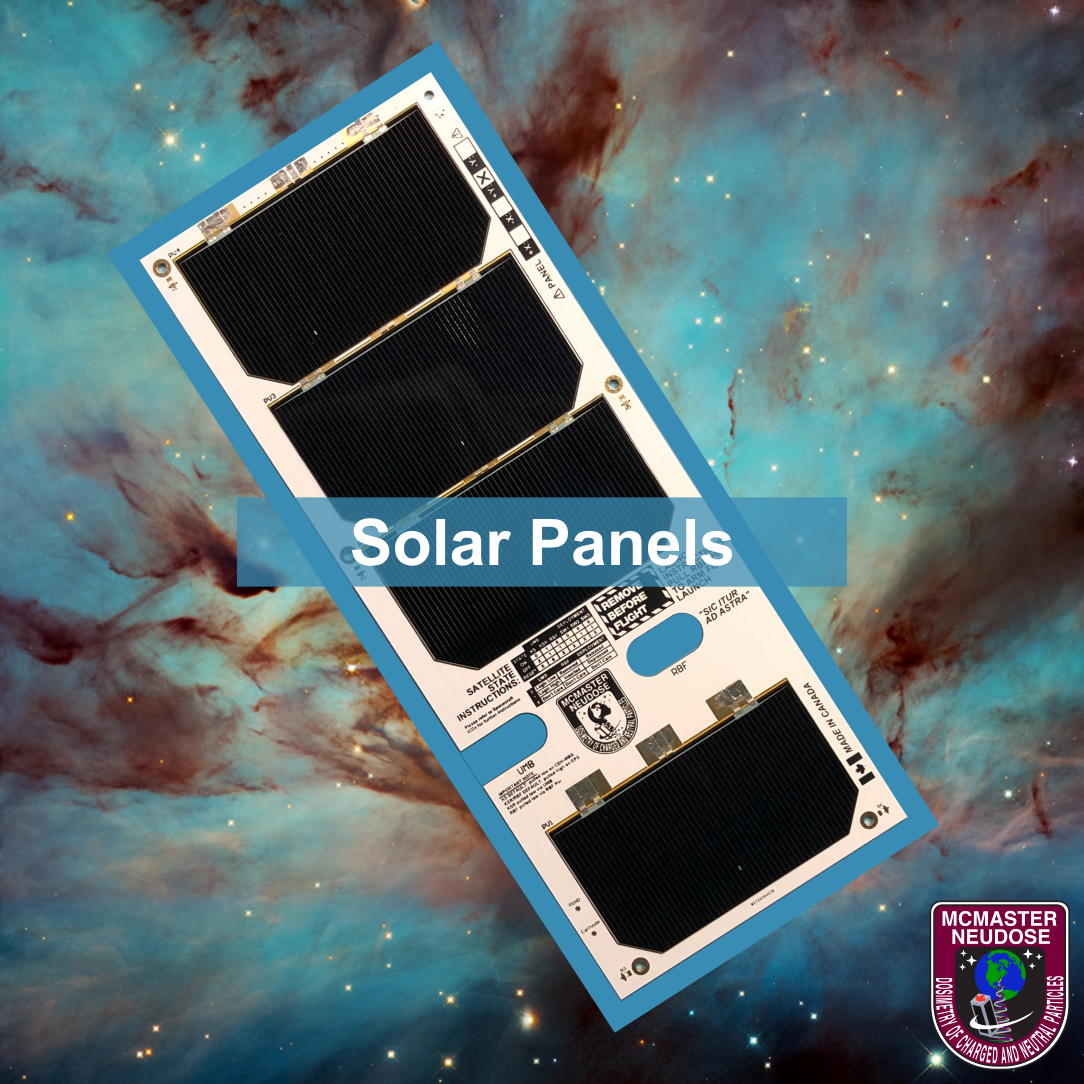
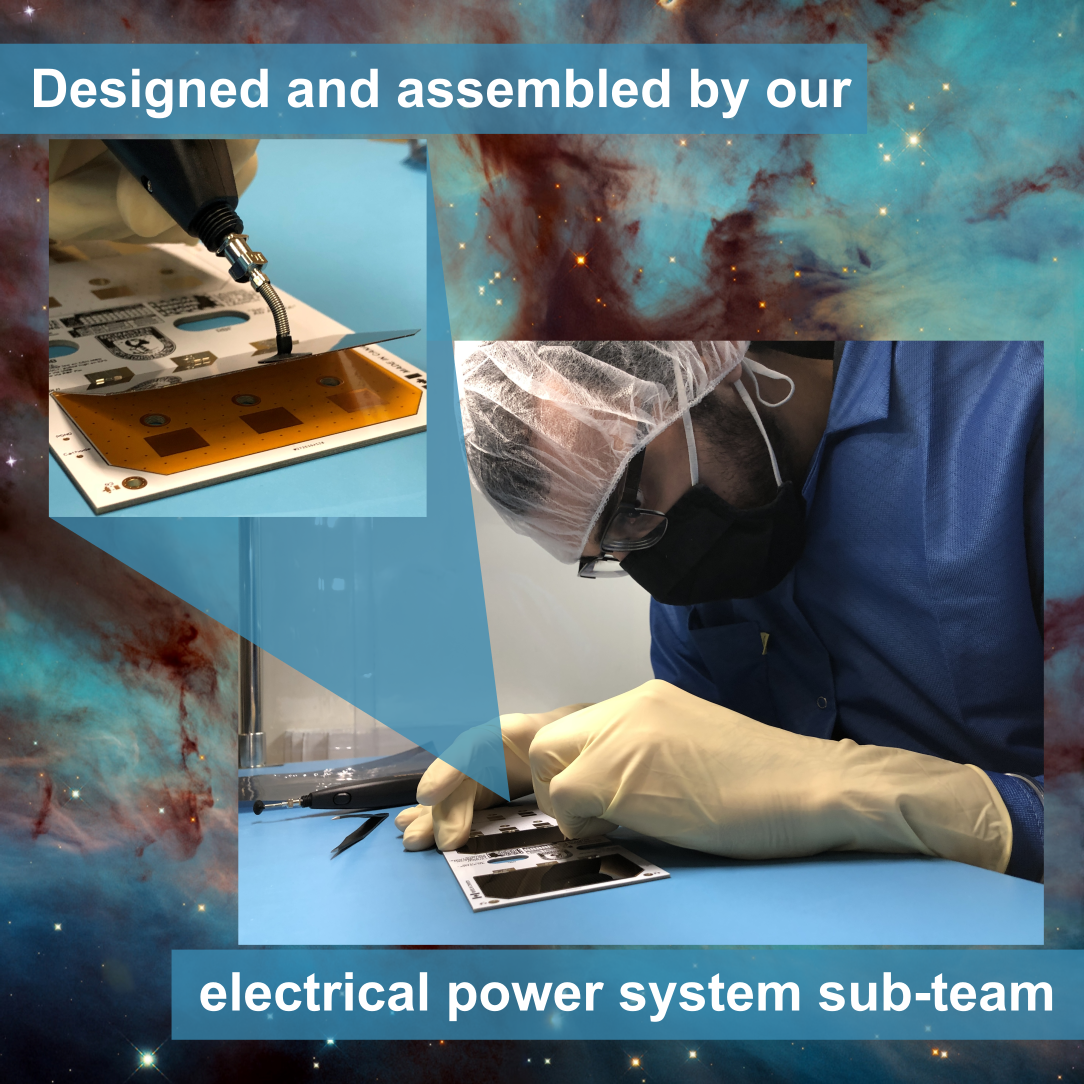
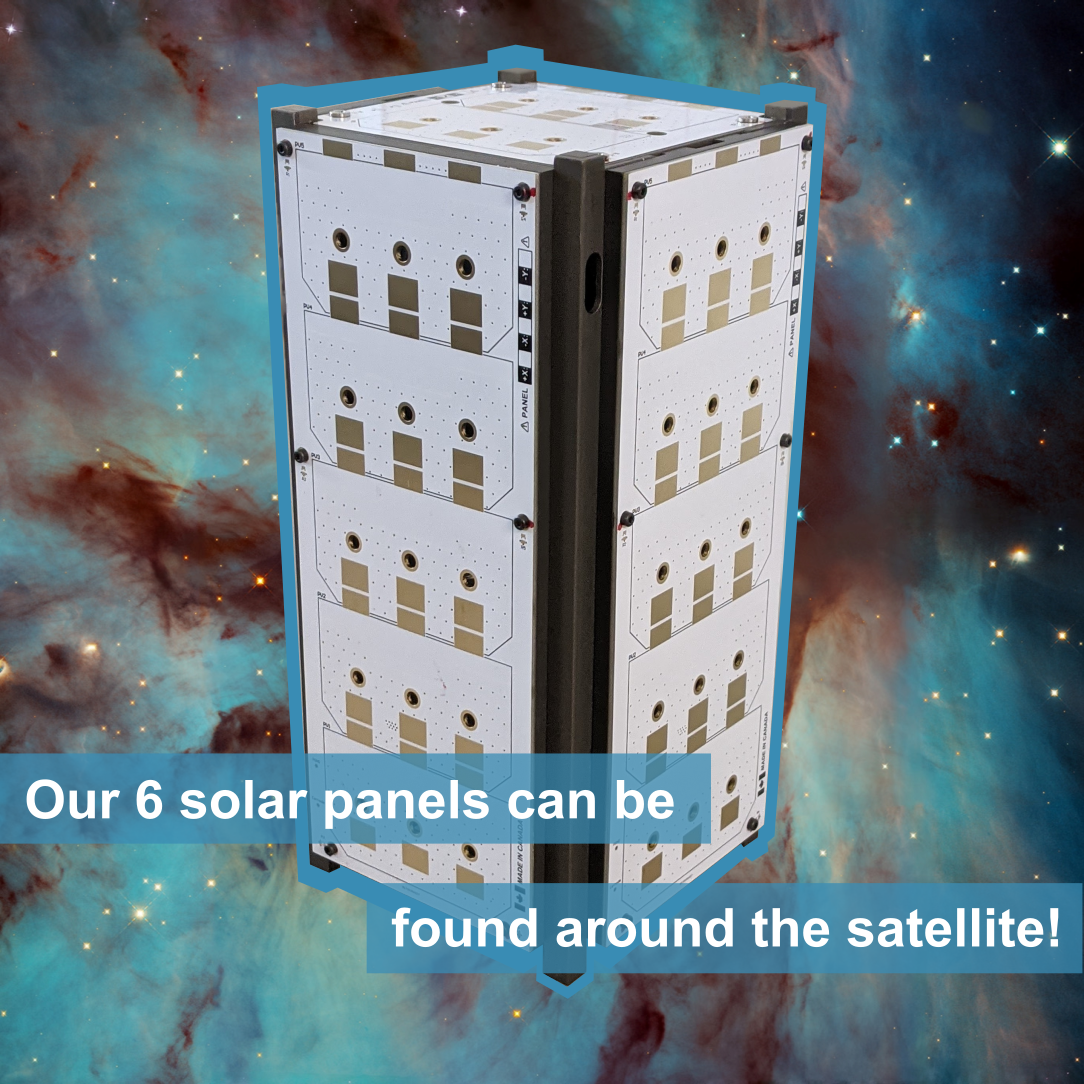
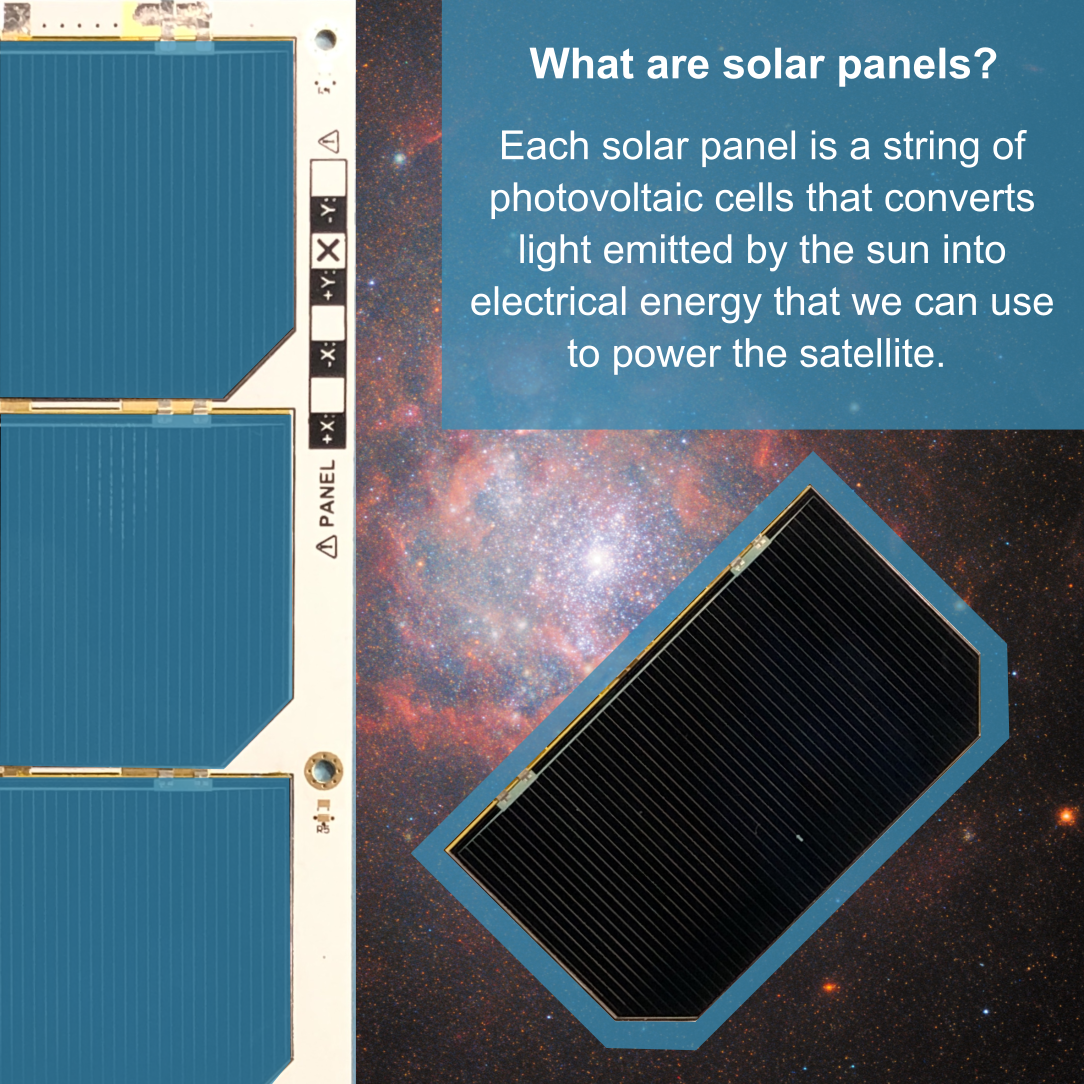
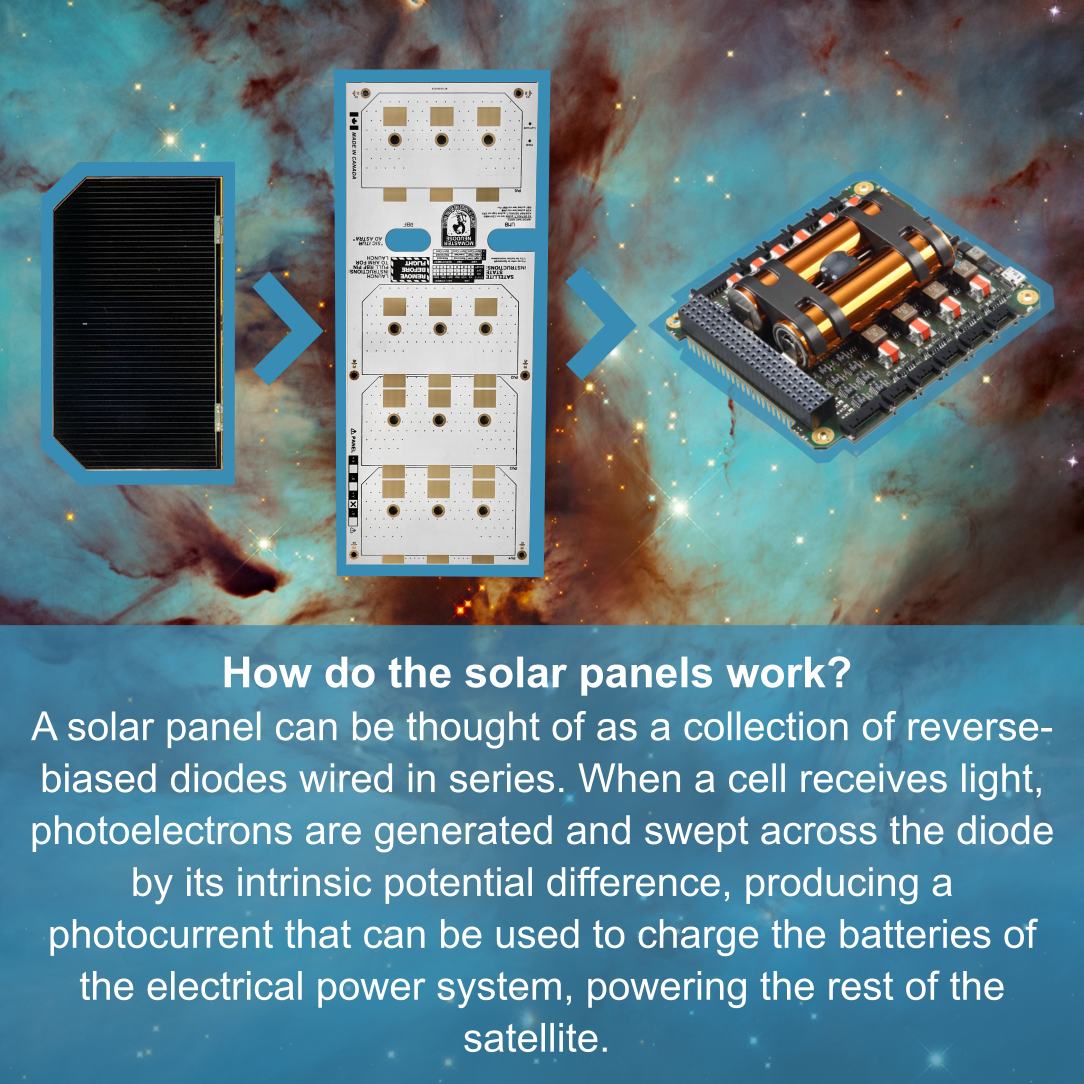
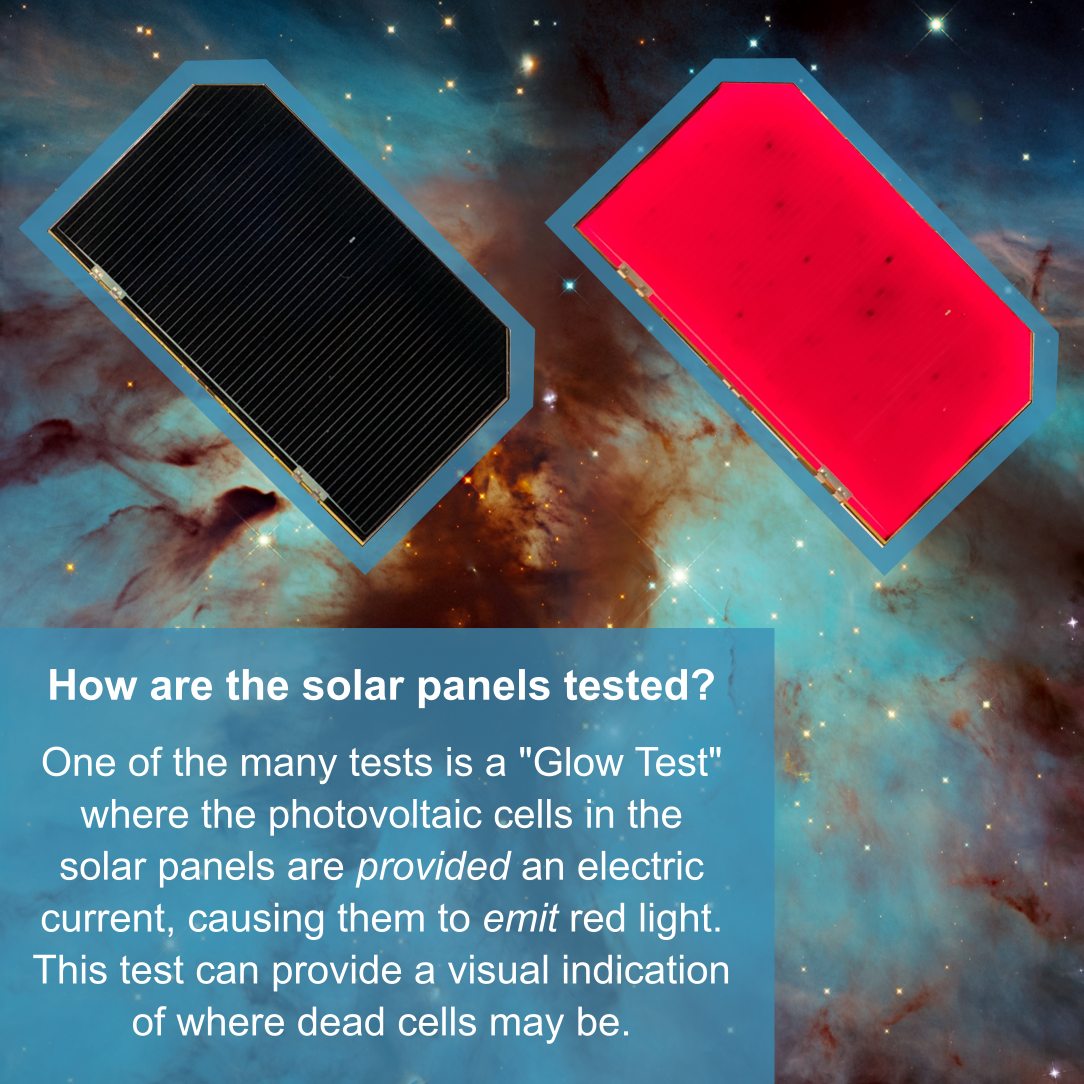
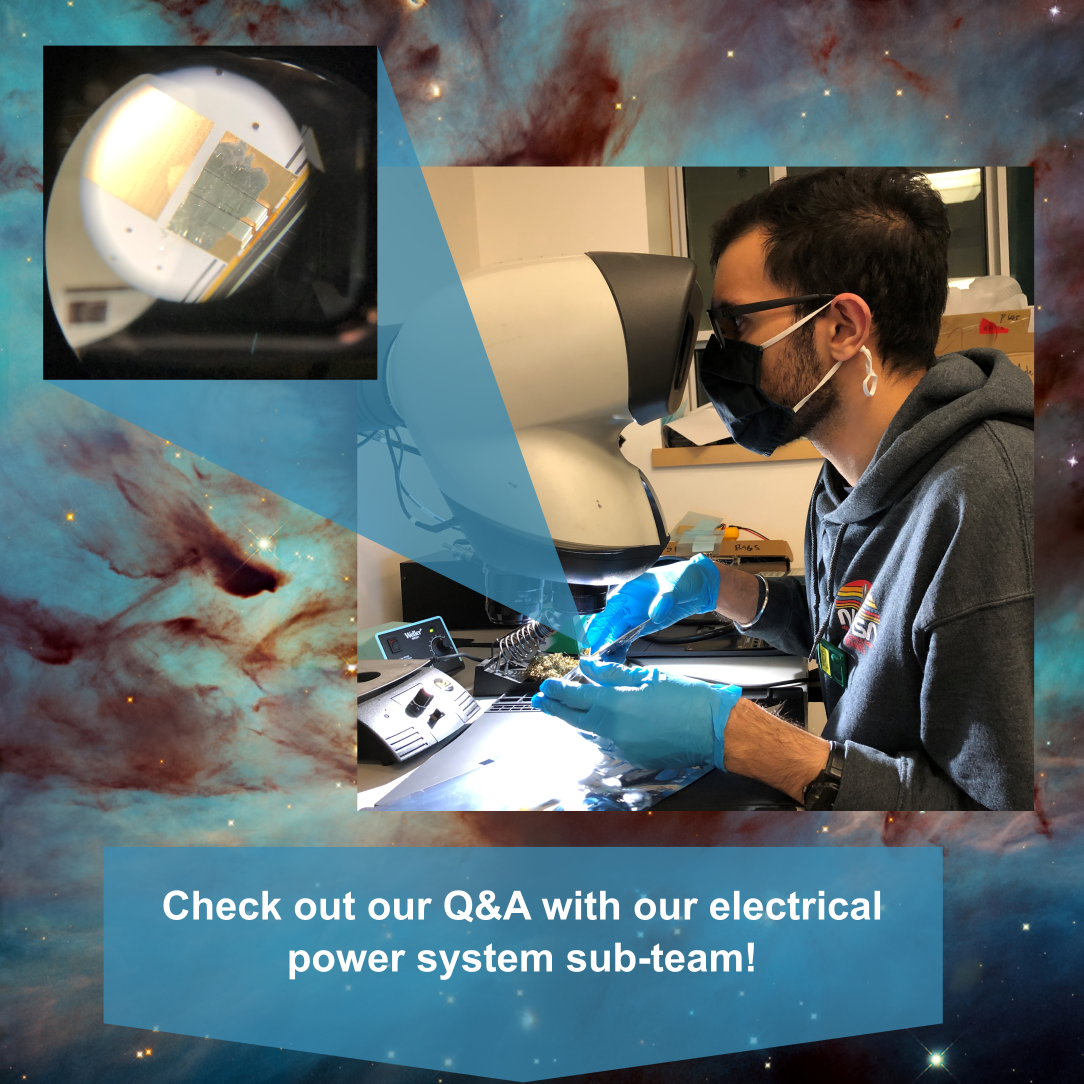
For this week's hardware blog post, we're introducing you to the solar panels which can be found all over our satellite! This component has been worked on by NEUDOSE's electrical power systems team. This team manages power generation using solar panels, power storage using batteries and the overall power distribution to sub-systems.
Check out our Q&A with our electrical power system team:
Q: How much of each Solar Panel was designed/assembled by the team, as opposed to bought commercially?
A: Each Solar Panel consists of a Printed Circuit Board (PCB) with 2-6 Solar Cells adhered to its surface, depending on which face of the satellite the panel is for. The Solar Panel PCBs were designed from scratch by our team, and sent to an external company for fabrication. The Solar Cells themselves were bought to our custom specifications from a commercial manufacturer. Our team then had to adhere the cells to the panels without breaking them, or getting them dirty, and make sure the assembled panel was functional.
Q: How do you know the Solar Panels will receive enough light to power the satellite for the entire mission?
A: Our Orbital sub-team has done extensive work in quantifying the trajectory of the satellite in orbit, and quantifying how much light each face of the satellite will be exposed to throughout. We made use of this information to customize our solar cells place them in as optimal of a location as possible.
Q: How do you test the Solar Panels before placing them on the satellite?
A: The first thing we check is that the tabs of the solar panel PCBs are electrically connected in series, as the cells should be. We then adhere the cells to the panel and characterize their performance electrically by measuring its open-circuit voltage and current, as well as environmentally by applying a calibrated light source against it and measuring the power it produces, generating what is known as a characteristic IV curve.
We hope you learned something new about mechanical structure hardware! Feel free to reach out if you have any questions about this hardware or NEUDOSE.